Rotary Dryer
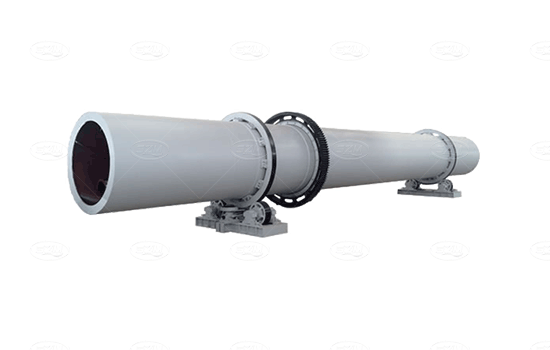
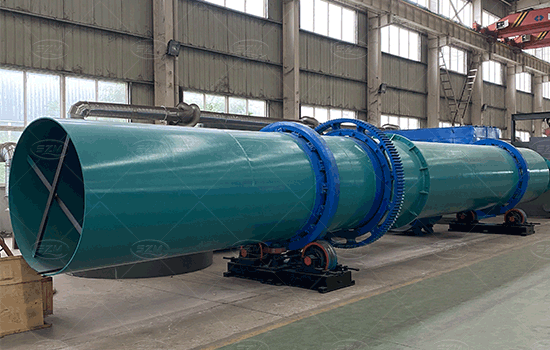
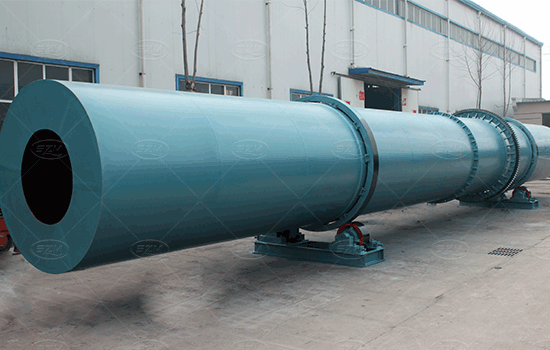
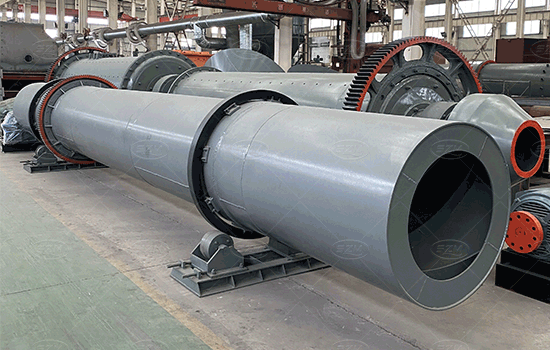
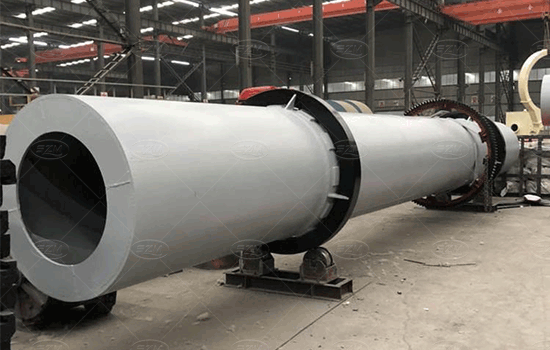
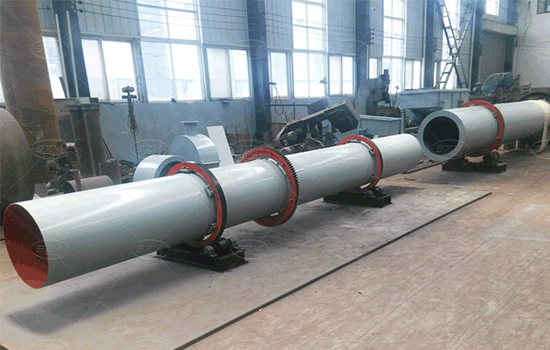
Rotary Dryer
Capacity:1-150(t/h)
Power:3-150(kw)
Weight:3-190(t)
Applied Materials:Slag, blast furnace slag, fly ash, cinder, slag, carbide slag, limestone, clay, sand, quartz sand, etc
Features and technology advantages of Rotary Dryer
Rotary dryer, also known as drum dryer or rotary dryer, is the most common and widely used dryer in mining equipment. It can be widely used for drying materials in coal industry such as slime, raw coal, flotation clean coal, mixed clean coal, etc; Drying of blast furnace slag, clay, bentonite, limestone, sand, quartz and other construction materials; Drying of various metal concentrates, waste slag, tailings and other materials in the mineral processing industry; And the drying of non-thermal sensitive materials in the chemical industry.
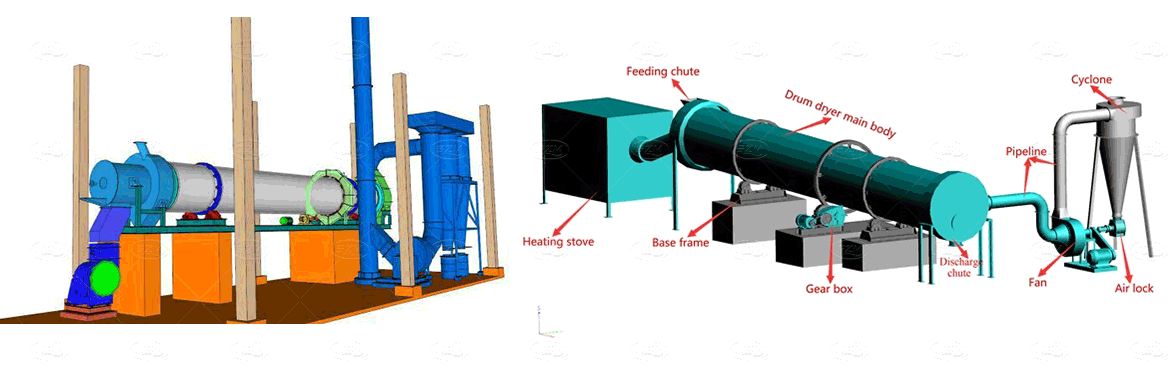
Rotary dryer is a kind of drying machine which can handle a large number of materials. Because of its reliable performance, flexible operation, strong adaptability and large capacity, rotary dryer is widely used in metallurgy industry, building materials industry, light industry, chemical industry, coal, mining industry and medicine industry. Rotary drum dryer is generally adapted to granular materials, and it can also be used for drying sticky and paste materials or materials with high water content.
Rotary dryer has the advantages of large capacity, wide application ranges, small flow resistance, large operation ranges, convenient operation, etc. It is commonly used for drying sand, slag, sludge, coal slime, limestone, quartz stone, granular material, powder material, paste material, compound fertilizer, chicken manure and cow dung.
Features of Rotary Dryer
1. High drying intensity and efficiency: due to the high air velocity, the materials are well dispersed in the gas phase, and the entire surface of the materials can be used as the effective drying area, so the limited drying area is greatly increased. At the same time, due to the dispersion and agitation during drying, the gasification surface is constantly updated, so the heat transfer process of drying is strong and efficient.
2. Advanced structure and strong drying capacity: the new internal structure strengthens the cleaning and heat conduction of the dispersed materials, eliminates the sticking phenomenon of the inner wall of the cylinder, and has stronger adaptability to the moisture and viscosity of the materials.
3. High degree of automation and high efficiency: computer automatic control is adopted, and different drying temperature and drying time can be configured according to drying requirements to realize drying automation. This can save manpower and material resources, thus improving the operation efficiency.
4. Large processing capacity, low drying cost: large processing capacity, high thermal efficiency. When the unbound water is dried, the thermal efficiency can reach 60%. The drying intensity is high. Because the material is highly dispersed in the air stream, the total surface area of particles is the effective area of drying, so the drying cost is low.
Working principle of Rotary Dryer
The heat source of the single-cylinder dryer comes from the combustion device, and the industrial dryer adopts the downstream heating mode. Therefore, the materials that need to be dried slip into the cylinder from the feed box and feed, and then are pushed to the rear by the spiral sheet. Due to the inclined placement of the dryer, on the one hand, the material flows to the rear under the action of gravity and rotation, on the other hand, the material is repeatedly picked up by the plate, carried to the upper end, and then continuously scattered, so that the material forms a uniform curtain in the cylinder, and fully exchanges heat with the hot air flow in the cylinder. As the material is repeatedly scattered, the moisture contained in the material is gradually dried, so as to achieve the purpose of drying.
Product Data
Technical Data of Rotary Dryer:
Specifications(m)
Cylinder volume
Capacity
Tilt angle
Maximum intake air temperature
Main motor power
Total weight
(diameter x length)
(m³)
(t/h)
(%)
(℃)
(kw)
(t)
Φ1.2×8.0
9
1.9-2.4
3-5
700-800
7.5
9
Φ1.2×10
11.3
2.4-3.0
3-5
700-800
7.5
11
Φ1.5×12
21.2
4.5-5.7
3-5
700-800
15
18.5
Φ1.5×14
24.7
5.3-6.6
3-5
700-800
15
19.7
Φ1.5×15
26.5
5.7-7.1
3-5
700-800
15
20.5
Φ1.8×12
30.5
6.5-8.1
3-5
700-800
18.5
21.5
Φ1.8×14
35.6
7.6-9.5
3-5
700-800
18.5
23
Φ2.2×12
45.6
9.7-12.2
3-5
700-800
22
33.5
Φ2.2×14
53.2
11.4-14.2
3-5
700-800
22
36
Φ2.2×16
60.8
13.0-16.2
3-5
700-800
22
38
Φ2.4×14
63.3
13.5-16.9
3-5
700-800
37
45
Φ2.4×18
81.4
17.4-21.7
3-5
700-800
37
49
Φ2.4×20
90.4
19.3-24.1
3-5
700-800
45
54
Φ2.4×22
99.5
21.2-26.5
3-5
700-800
45
58
Φ2.6×24
127.4
27.2-34.0
3-5
700-800
55
73
Φ3.0×20
141.3
30.1-37.7
3-5
700-800
75
85
Φ3.0×25
176.6
37.7-47.1
3-5
700-800
75
95
Φ3.2×25
201
42.9-53.6
3-5
700-800
90
110
Φ3.6×28
285
60.8-76.0
3-5
700-800
160
135